Inventory and Material Management Professional
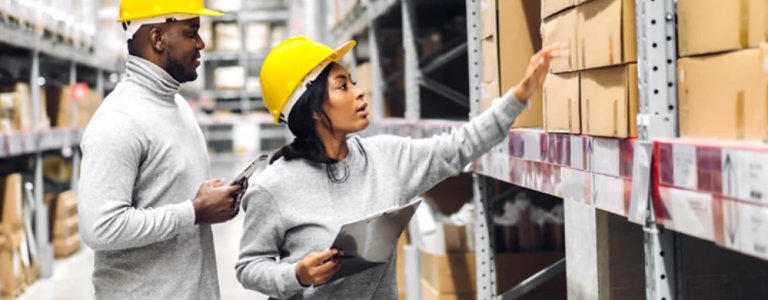
- Overview
- Curriculum
- Instructor
Inventory and Material Management Professional course aims to equip you with a comprehensive understanding of the principles, strategies, and tools necessary to effectively manage inventory and materials within an organization, ultimately contributing to improved operational efficiency and cost savings. Here’s a general outline of what this course might cover:
Learning objectives
In this course, you will learn:
Learning objectives
In this course, you will learn:
- Inventory and materials management techniques.
- Inventory valuation and optimization.
- Concepts of Material Requirement Planning (MRP).
- Measuring and evaluating inventory performance.
- Apply lean principles to inventory and material management.
- Team leadership and collaboration.
UNIT 1
Introduction to Inventory Management
- Lesson 1: Definition and importance of inventory management
- Lesson 2: Objectives and goals of inventory management
- Lesson 3: Types of inventories: raw materials, work-in-progress, finished goods, MRO (maintenance, repair, and operations), etc.
- Key terminology and concepts
UNIT 2
Inventory Planning and Forecasting
- Lesson 1: Forecasting methods: qualitative, quantitative, and time series analysis
- Lesson 2: Demand forecasting techniques
- Lesson 3: Inventory control models: EOQ (economic order quantity), ABC analysis, JIT (just-in-time), etc.
- Lesson 4: Inventory planning strategies: safety stock, reorder points, lead time management
UNIT 3
Inventory Optimization
- Lesson 1: Inventory turnover ratio and its significance.
- Lesson 2: Inventory carrying costs
- Lesson 3: Minimizing holding costs and stockouts
- Lesson 4: Vendor-managed inventory (VMI) and consignment inventory
- Cross-docking and dropshipping
UNIT 4
Inventory Management Systems
- Lesson 1: Introduction to inventory management software.
- Lesson 2: Features and functionalities of popular inventory management systems
- Lesson 3: Implementation and integration considerations
- Lesson 4: Warehouse management systems (WMS) and their role in inventory control
UNIT 5
Materials Management
- Lesson 1: Material planning and procurement.
- Lesson 2: Supplier selection and evaluation
- Lesson 3: Negotiation tactics and contracts management
- Inventory valuation methods (FIFO, LIFO, weighted average)
UNIT 6
Risk Management and Compliance
- Lesson 1: Inventory risk assessment.
- Lesson 2: Regulatory compliance (e.g., FDA regulations for pharmaceutical inventory)
- Lesson 3: Inventory security and loss prevention
- Lesson 4: Business continuity planning for inventory disruptions
UNIT 7
Performance Measurement and Continuous Improvement
- Lesson 1: Key performance indicators (KPIs) for inventory management
- Inventory audit and reconciliation processes.
- Lesson 3: Lean inventory management principles
- Lesson 4: Six Sigma and DMAIC (Define, Measure, Analyze, Improve, Control) methodology for process improvement
UNIT 8
Project Management for ERP Implementations
- Lesson 1: Project planning, scoping, and resource allocation.
- Lesson 2: Execution and monitoring of ERP implementation projects.
- Lesson 3: Risk management and issue resolution
- Lesson 4: Post-implementation evaluation and continuous improvement
UNIT 9
Final Project or Capstone
- Lesson 1: Application of knowledge and skills acquired throughout the course.
- Lesson 2: Planning and executing a mock ERP implementation project.
- Lesson 3: Presentation of findings and recommendations.
UNIT 10
Certification Exam Preparation
- Lesson 1: Review of key concepts covered in the course.
- Lesson 2: Practice exams and quizzes.
- Lesson 3: Exam-taking strategies and tips.
- Conclusion
- Exam
This course includes:
Duration: 10 Weeks